Glossing must be OFF to simplify creating 90 Degree Corners
Monday, September 16, 2024
90 Degree Routing - Glossing Off
Saturday, September 14, 2024
Ethernet PHY - Length Matching
Ethernet PHY PCB Design Layout Checklist
The total length of each MDI trace should be less than 2 inches, or 2000 mils.
The traces should be lengthmatched within 20 mils for 1G transmissions and within 50 mils for 100M or 10M transmissions.
The number of vias and stubs on the MDI traces should be kept to a minimum.
The traces should be length- matched within . . .
20 mils for 1G transmissions
50 mils for 100M or 10M transmissions.
ISSI SRAM/SDRAM Layout Guide
See . . .
AN42S01.AN - ISSI SRAM/SDRAM Layout Guide
Using SDRAM vs. DDR RAM in Your PCB Design | Blog | Altium Designer
ISSI DDR3 SDRAM Layout Guidelines (Download PDF)
Tuesday, May 7, 2024
Nine Dot Connects - Library Services
If you are looking for professional Altium Library design services and have a budget that can support the service then I highly recommend taking a look at . . .
Nine Dot Connects - Library Services
If you have a limited budget and like to do things yourself then I recommend you take Parts for free test drive.
Link to Parts https://pcbparts.blogspot.com/p/welcome.html
Parts is a Scalable Database Library Managment Solution for Altium users.
Parts can be used to quickly create and manage an Access or MySQL Database Library.
To request technical support or a Free Parts online demonstration contact me at Parts.
Link: Contact Parts
Thank you for your support
Randy Clemmons
Routing Options - Explained
Interactive Routing Options - Online Altium (Login Required)
Gloss Effort (Routed) and Gloss Effort (Neighbor).
You may think of Gloss as a postprocessor: after the trace is put in and conflicts resolved, it straightens the result to get rid of corners and other uglies.
If it is Off, uglies are preserved, if Weak - the geometry of the trace mainly preserved, just locally smoothed, if Strong - the trace is made pretty much as short as possible.
See the pictures. Thin white line in all cases shows the trace as it was initially put in, thenthe first picture shows how it came out after conflict resolution, Gloss (Routed) Off
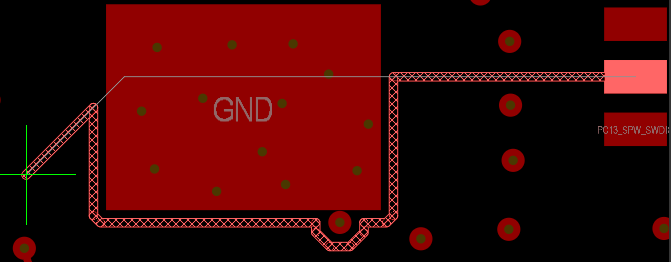
the second - removed sharp corners and small jogs, Gloss (Routed) Weak
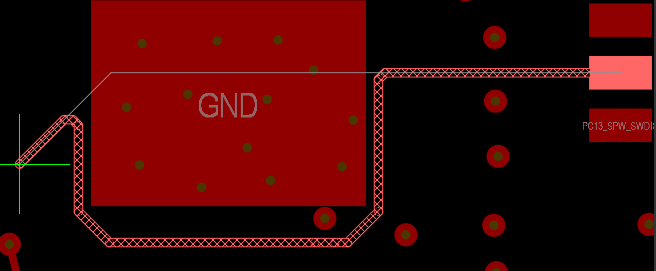
the third - tightened it, Gloss (Routed) Strong.

In addition to this, notice that not only the trace being routed may need improvement after conflict resolution, but also its neighbors, if they got pushed:
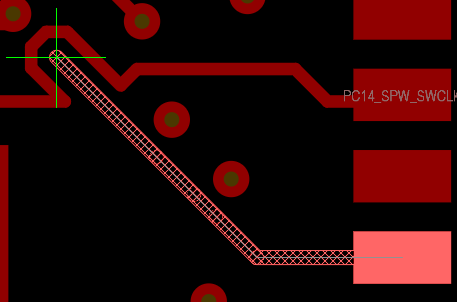
Again, the same three levels of Glossing are possible, and that is controlled By Gloss Effort (Neighbor) setting.
This is a small option. It controls what happens when during routing you click on a target to complete a connection.
Controls Pad Entry, which is also the responsibility of Gloss (no Pad Entry if Gloss (Routed) is Off)
In this picture you see the thin white line showing the trace that was originally put in, and the final result, where Gloss improved the pad entry.

You may not think much of this improvement, but consider also these two cases:

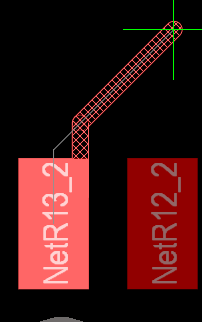
Here keeping the middle entry caused a nasty acute angle at pad edge, and shifting it to the side is probably welcome.
So, Pad Entry Stability setting tells Gloss how close the corner has to be to the pad edge when shifting entry sideways becomes allowed.
This is related to Trace Centering option.
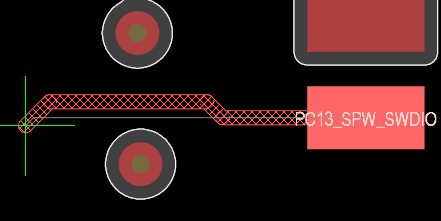
Otherwise the trace will be put at (normal + additional) clearance from obstacles, so in this case it will be not so much "trace centering" as "preferred clearance".
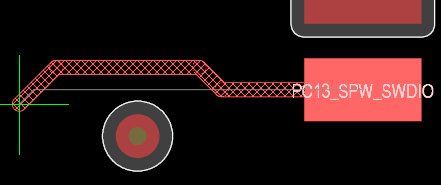
The value of the additional clearance, is controlled by Added Clearance Ratio.
Consider the case when after a click while routing, you make a sharp turn.
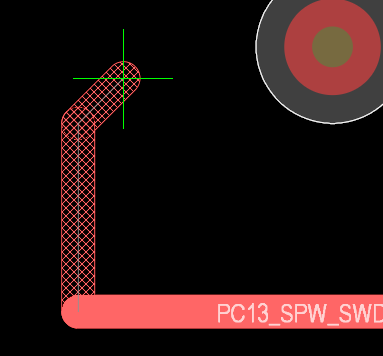
Not everyone likes to have those right angles in their traces, which is when the miters come to the rescue - also the responsibility of Gloss.
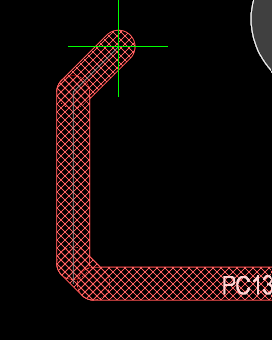
Here the white thin line starts from the click point, but as you can see, a small portion of the previously committed trace is cut off and a short diagonal segment is inserted.
Miter Ratio controls the length of the miters used by the router. Since miters can be arcs as well as segments, they are defined in terms of "sharpest turn radius" as a multiple of trace width.
Miter Ratio 1 allows the radius equal to trace width, which can be plainly seen for arcs:

and not so plainly, but still true, for tracks:

Thursday, May 2, 2024
Back Drill
Design > Layer Stack Manager > Menu Back Drills
Saturday, April 20, 2024
0.5mil Length Matched Diff Pairs
Customer's Requirements for 0.5mil Length matched Signals within the pairs.
Example
Sawtooth settings based on 6mil / 6mil (trace / gap) Diff Pair
Tip:
You have to select the type of tuning before you start tuning a net.
Hit Tab Key before you start the length matching
Thank you Wayne :)
Saturday, February 17, 2024
Find and Fix Corrupt Mid Layers
Example six layer board with Corrupted Mid Layer IDs.
.Layer_ID and .Layer_Name
Example . . . Corrupt Mid Layer IDs
The Fix . . .
Backup the Project Design Files using Project > Project Packager
Open the PcbDoc . . .
Import Changes from Project to Update the Netlist and Design Rules in the PcbDoc.
Run DRC checks, take note of any reported errors.
Create and open a Copy of the PcbDoc in the project.
Design > Layer Stack Manager
Export Stackup as CSV, then include Impedance Screen Captures in Excel.
Delete all Mid Layers from the Corrupt Stackup.
Then add Mid Layers as needed.
Save Stackup to the PcbDoc, then check Mid Layer IDs and Layer Names.
Example Corrected Mid Layer IDs.
Design > Layer Stack Manager
Enter Material Thickness and Impedances as needed.
Save the fixed Stackup to the copy of the PcbDoc
Copy each Mid Layer from Original PcbDoc to Copy of PcbDoc.
Suggested Selection Filter Settings for Copying Mid Layers
Show all Mid Layers and use Signal Layer Mode.
Hide the Multi-Layer to avoid Selecting the Board and Board Cutouts.
Copy each Mid Layer from the Original PcbDoc to Copy of PcbDoc.
Use Edit > Paste Special > Check Paste on Current Layer and Keep Net Name.
Edit Design Rules and Fix Trace Width Rules as needed, including Diff Pairs.
Import Changes from Project to update the Netlist and Design Rules in the Copy.
Run DRC checks, take note of any reported errors.
Done !
Friday, February 16, 2024
Thursday, February 15, 2024
Footprint Expert Surface Mount Families - PCB Libraries
Microsoft Word - Footprint Expert Surface Mount Families
Use the link above to download the 39 page PDF
That's it
Friday, February 9, 2024
Variants - Silkscreen and Solder Paste
Project > Variants
Check the First Option for Silkscreen
Check Both Options for Solder Paste
That's it !
Project Releaser - Temp Files Location
Thursday, February 1, 2024
Room - Donut Shaped with Height Constraint
Example - Donut Shaped Room with Height Constraint
Height Constraint using Keep Objects Outside
Create two Arcs with Crosshairs.
Draw Rectangular Room, ignore self-intersecting warnings while drawing the polygon. Then Edit Polygon Room Vertices to form joined 90 degree Arcs using Snap to Lines and Arcs.Notes:
Height Constraint Syntax - AsMM(Height) > 0.6
Height Constraint - Online DRC does NOT work (bug ?)
Height Constraint - Batch Mode DRC Check works.
Use Shift + Space Bar to Pull Lines to Arcs.